Le défi de l’électrique sur les machines de chantier passe par l’innovation
Les fabricants d'équipements de construction, dont le marché s'élève à 200 milliards de francs, sont confrontés à un défi complexe. Ils doivent réduire considérablement leur dépendance à l'égard du carburant diesel et passer à des technologies à plus faibles émissions. Dans le même temps, ils doivent continuer à fournir les performances que leurs clients attendent, tout en veillant à leur rentabilité.
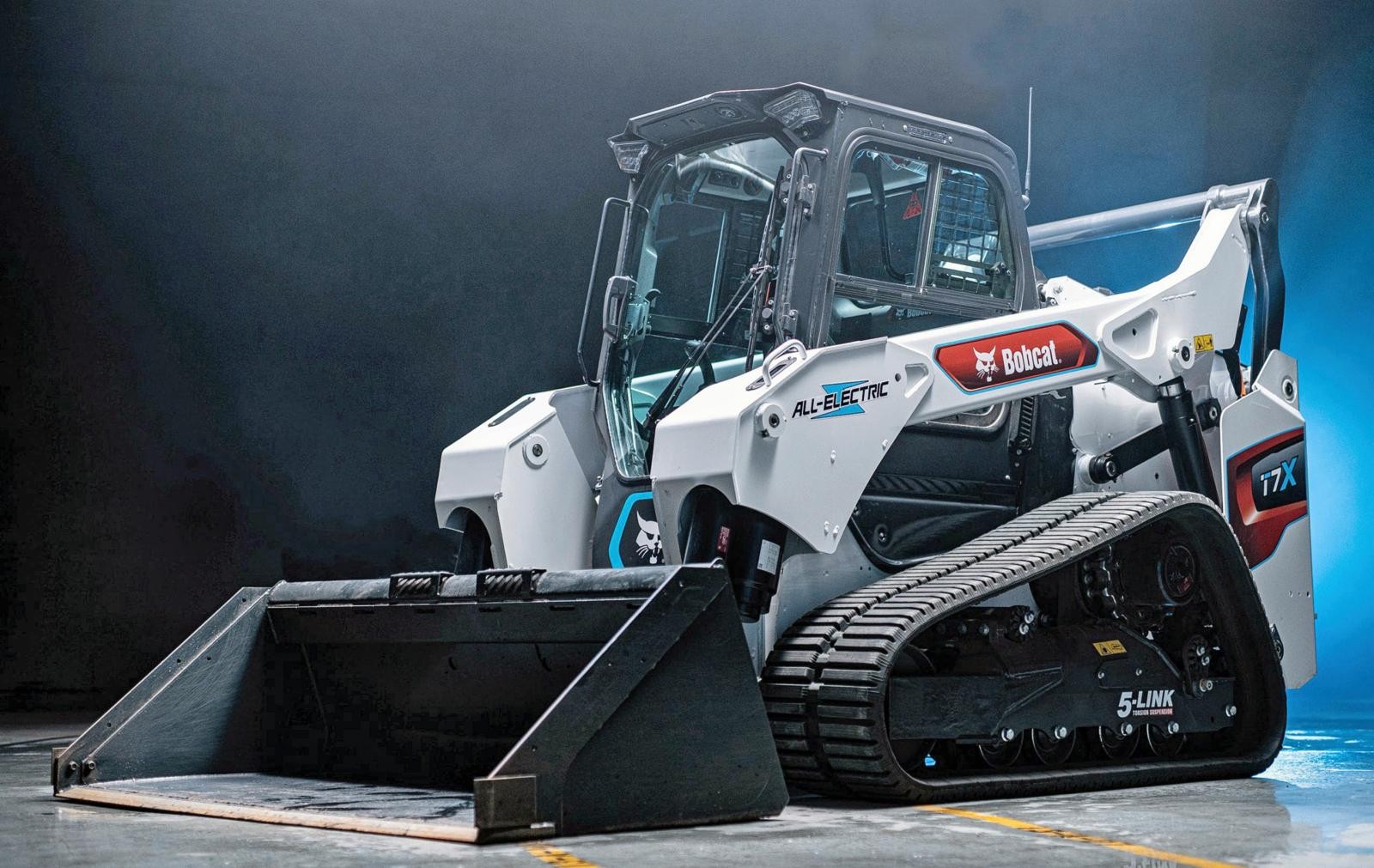
Crédit image: Doosan Bobcat
La Bobcat-T7X est équipée d’une batterie de 62 kWh. Si le véhicule avait employé l'hydraulique, la batterie aurait dû avoir une capacité de plus de 300 kWh pour offrir la même endurance.
Pour remplir les mêmes tâches que les machines diesel équivalentes, les éléments du groupe motopropulseur des véhicules de construction électriques doivent être dimensionnés pour offrir les mêmes performances, indique la société d’analyse IDTechEx dans un nouveau rapport. Par conséquent, la clé du déploiement des machines électriques est la compréhension de leur cycle de travail quotidien typique et de leurs besoins en énergie. Comme le secteur de la construction utilise toute une série de machines mobiles tout-terrain différentes, la puissance maximale requise pour le moteur varie considérablement en fonction de l'application et de la taille de la machine.
De même, le besoin énergétique quotidien total est régi par l'utilisation de la machine, certains cycles d'utilisation ne nécessitant qu'un fonctionnement sporadique pendant la journée, tandis que d'autres machines fonctionnent presque en continu. Des systèmes modulaires sont nécessaires pour optimiser les performances et le coût de ces engins électriques.
Le défi de la
recharge
La plupart des fabricants, en particulier aux Etats-Unis et en Europe, ont
concentré leurs premiers travaux de développement en matière d'électrification
sur les machines de construction compactes. Leur petite taille et les exigences
relativement légères en matière de cycle de travail signifient qu'une journée
de travail de 8 heures peut être assurée avec une taille pratique de batterie Lithium-ion
(< 50 kWh) et de moteur électrique (< 20 kW).
Plusieurs voies pour la recharge de ces machines sont en cours d'exploration: les grandes batteries, qui peuvent assurer une journée de travail complète sans recharge, les modèles plus petits avec possibilité de recharge rapide pendant la journée de travail, le fonctionnement par câble captif et l'échange de batteries. La taille optimale de la batterie pour chaque machine devra tenir compte de facteurs tels que le coût élevé des batteries tout-terrain, l'impact de la charge rapide sur l'autonomie, la disponibilité d'une alimentation électrique régulière et le coût de l'installation d'une infrastructure de charge sur les chantiers.
Problème de
taille
Si les petites machines sont le point de départ naturel de l'électrification
sur ce marché, ce sont les machines de construction plus lourdes qui
contribuent le plus aux émissions de CO2 du secteur. Il est essentiel que les
équipementiers proposent également des solutions zéro émission pour ces
véhicules de plus grande taille. Le problème réside dans le fait que des machines
telles que les grandes excavatrices peuvent demander plus de 75 kWh d'énergie
par heure de fonctionnement. Cela signifie qu'il faut installer une énorme batterie
là où un poste de travail continu de 8
heures est demandé. Les prix actuels des batteries Lithium-ion pour véhicules lourds
hors route étant de l'ordre de 600 fr. et plus par kWh, ces batteries ont un
coût extravagant.
La manière dont les grosses machines sont rechargées est essentielle pour réduire les besoins en capacité de la batterie. Différentes approches sont à l'étude. Par exemple, de nombreux équipementiers chinois ont opté pour une méthode de charge rapide en courant continu à deux pistolets, qui permet d'ajouter 300 kWh pendant la pause repas. La société néerlandaise Urban Mobility Systems a mis au point un système d'échange de batteries utilisant trois modules de 130 kWh. Ce dernier système a été testé dans de grandes excavatrices Doosan et Hyundai.
L'amélioration de l'efficacité du groupe motopropulseur sera également cruciale. Presque toutes les machines de construction électriques actuelles ont remplacé le moteur diesel par des batteries et des moteurs électriques, mais elles utilisent toujours un système hydraulique standard, dont le rendement stagne à 30 %. Pour remédier à ce problème, des entreprises telles que Danfoss développent une technique hydraulique numérique qui améliore l'efficacité du groupe motopropulseur et réduit la consommation d'énergie, ce qui permet d'utiliser une batterie plus petite pour effectuer les mêmes journées de travail.
L'objectif final des machines de construction électriques est la mise en place de systèmes entièrement électriques, qui remplacent les systèmes hydrauliques et utilisent à leur place des actionneurs et des moteurs d'entraînement électriques. Doosan Bobcat a lancé une chargeuse à chenilles entièrement électrique, la T7X, au CES 2022. Développé avec Viridi Parente et Moog, l'amélioration de l'efficacité du système tout électrique permet d'utiliser une batterie de 62 kWh alors que, si le véhicule avait employé l'hydraulique, la batterie aurait dû avoir une capacité de plus de 300 kWh pour offrir la même endurance. Il faudra poursuivre les travaux de développement au cours de la prochaine décennie pour que les systèmes entièrement électriques soient déployés à plus grande échelle. Les actionneurs électriques sont actuellement coûteux et ne sont pas encore en mesure de répondre aux exigences des grandes machines de construction.
Marché à cent
milliards par an
On le constate, l'innovation est plus que
jamais nécessaire pour réaliser l'électrification dans ce secteur
difficile, et les entreprises avant-gardistes engagent déjà des efforts et des
ressources pour relever ces défis. IDTechEx prévoit que la part électrique du marché
des véhicules de construction représentera près de 100 milliards de francs par
an d'ici 2042.